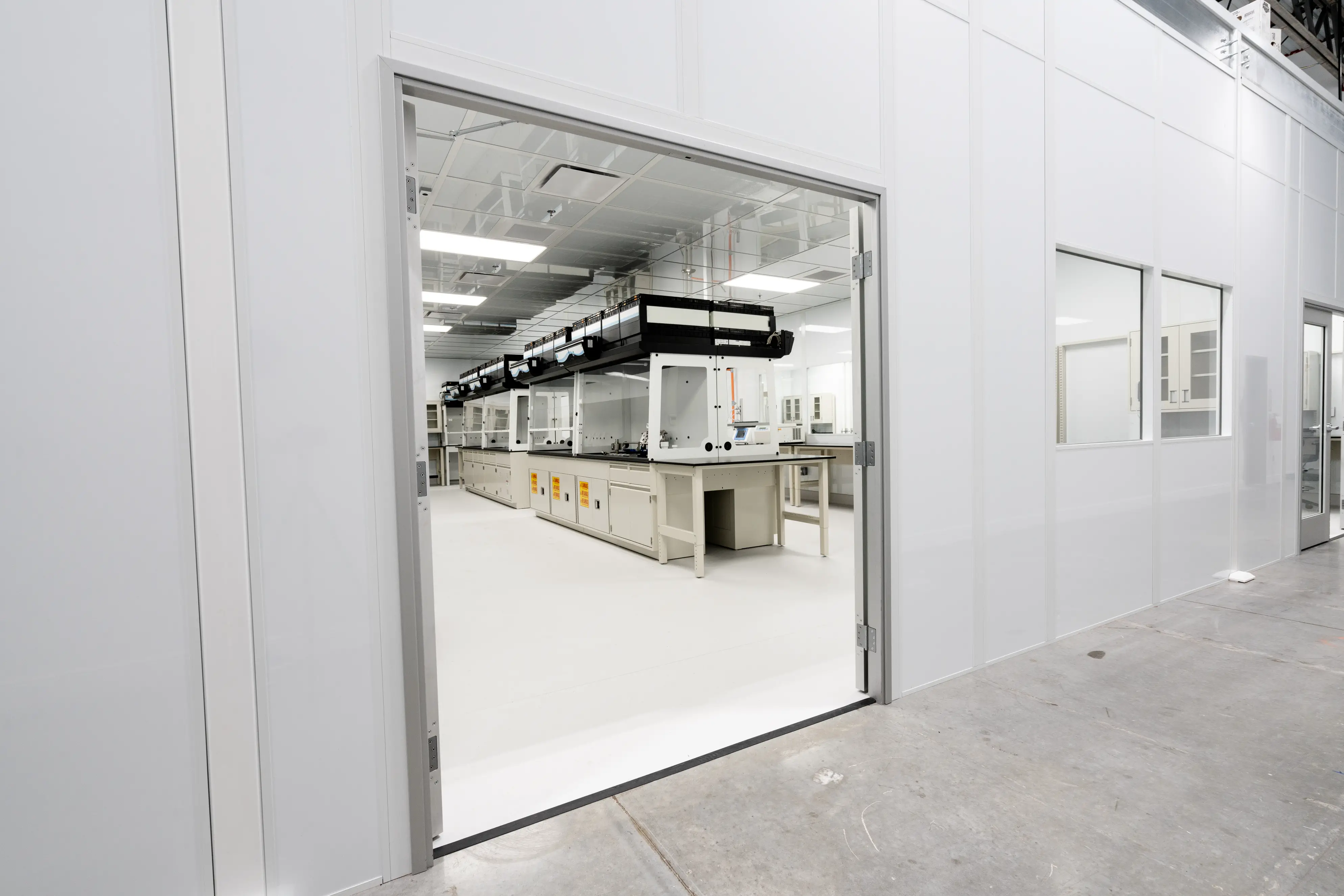
Aseptic Processing in Cleanrooms
In the realm of pharmaceuticals, biotechnology, and healthcare industries, the manufacturing of sterile products demands an unparalleled level of precision and purity. Aseptic processing refers to the meticulous technique of handling, preparing, and packaging sterile products to prevent any contamination by harmful microorganisms. ICS cleanrooms play a pivotal role in creating and maintaining these controlled environments that facilitate aseptic manufacturing.
What is Aseptic Processing?
Aseptic processing revolves around the concept of maintaining a "sterile chain of custody" from the initial stages of production to the final packaging. This means that every step of the manufacturing process must be conducted in a manner that eliminates the risk of contamination.
The process begins with the meticulous cleaning and sterilization of equipment, facilities, and personnel involved in manufacturing. This step is essential as even a single microbial contaminant can compromise the entire product batch. Once the controlled environment (cleanroom) is established, sterile ingredients are combined in a way that prevents any microbial introduction. Aseptic processing often utilizes specialized technologies like barrier systems, isolators, ISO 5 Cleanrooms, biological safety cabinets and restricted access barrier systems (RABS) to ensure that the products are shielded from potential contaminants during handling and filling processes.
Importance of Preventing Contamination:
Any microbial contamination can compromise the safety and effectiveness of medical products, putting patients' lives at risk. Contaminated pharmaceuticals can lead to severe health complications, adverse reactions, and, in some cases, even fatalities.
Contaminated products can also result in significant financial losses for pharmaceutical companies due to costly recalls, regulatory penalties, and damage to their reputation. Therefore, adhering to aseptic processing techniques is not just a matter of compliance but also a strategic measure to uphold the highest quality standards and protect public health.
The Role of Cleanrooms in Aseptic Processing
Cleanrooms are purpose-built environments where the concentration of airborne particles, such as dust, bacteria, and other microorganisms, is rigorously controlled. Our specialized facilities offer a tightly regulated atmosphere, ensuring that the production of sterile pharmaceuticals takes place in an environment free from potential contaminants.
Purpose of Cleanrooms in Minimizing the Risk of Microbial Contamination
The primary objective of cleanrooms in aseptic processing is to prevent any contamination from entering or spreading within the manufacturing area. As pharmaceutical products are highly sensitive to even the tiniest microbial presence, cleanrooms serve as a protective shield against external pollutants that could compromise product quality and patient safety.
Key Features of our Cleanrooms
Our cleanrooms are designed with meticulous attention to detail, incorporating critical features to maintain the highest levels of cleanliness and sterility. Some of these features include state-of-the-art air filtration systems, temperature and humidity control, equipment integration, anteroom for proper gowning, and many custom add-ons such as sinks, laminar flow hoods, biological safety cabinets and much more.
How Cleanrooms Contribute to Product Stability
The controlled environment of ICS cleanrooms plays a pivotal role in preserving the integrity, stability, and shelf life of pharmaceutical products. By maintaining sterile conditions throughout the production process, the risk of product degradation is significantly reduced. Cleanrooms help prevent unwanted reactions, microbial growth, and chemical degradation that can occur when products are exposed to contaminants during manufacturing, allowing companies to deliver products of the highest quality.
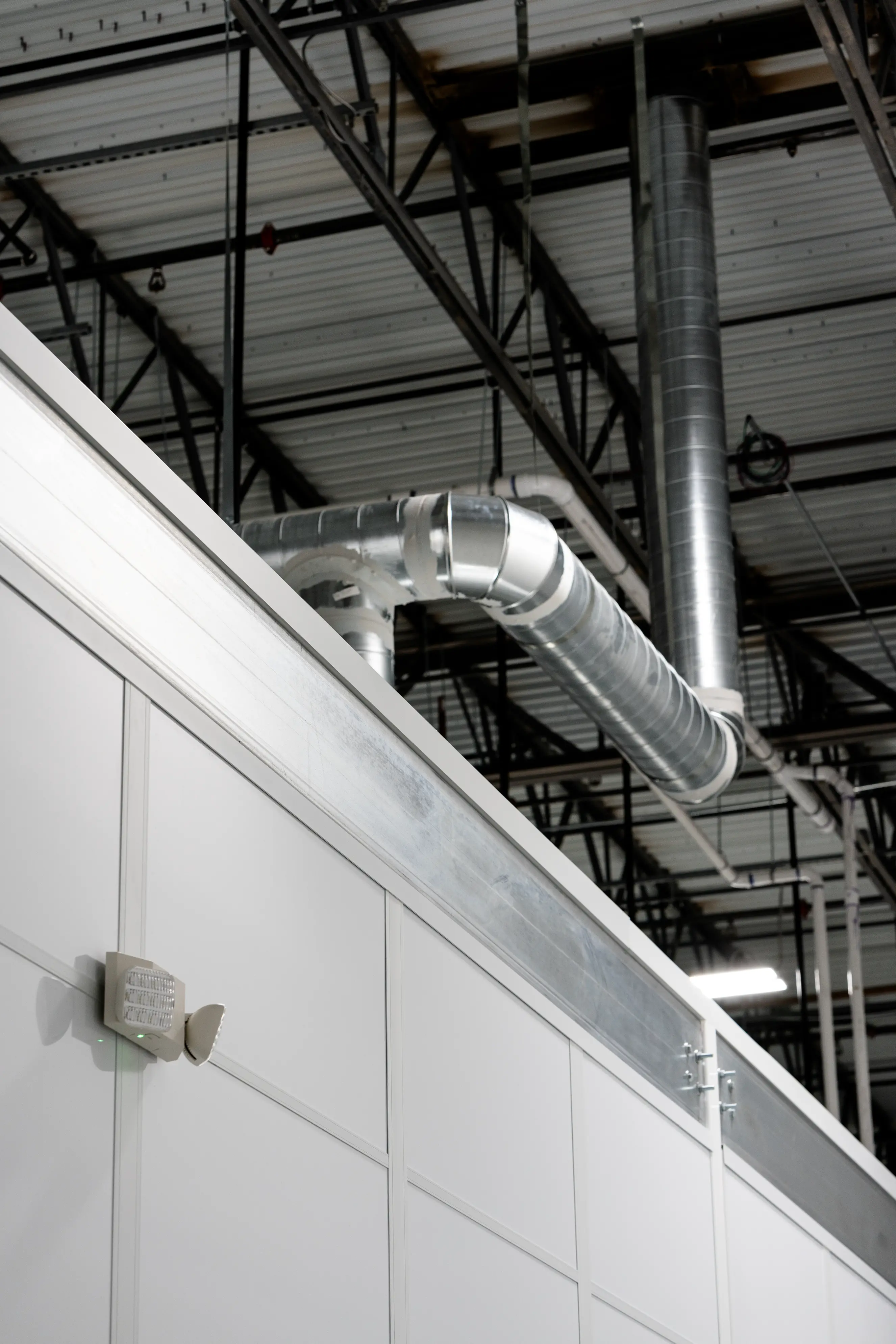
Best Practices for Aseptic Processing in Cleanrooms
Personnel Training
Personnel involved in aseptic processing play a pivotal role in contamination prevention. They are essentially the guardians of cleanrooms, responsible for maintaining the sterile environment throughout the manufacturing process. It is imperative that all personnel undergo rigorous training to ensure they fully understand the principles of aseptic techniques. Training programs should cover a range of topics, including proper gowning procedures, aseptic behavior, and contamination control measures. Personnel should also be educated on the potential consequences of contamination and the critical role they play in upholding the highest quality standards. Regular refresher courses and ongoing training are essential to keep personnel up-to-date with the latest industry practices and maintain a culture of compliance.
Environmental Monitoring
Continuous environmental monitoring is an integral part of aseptic processing in cleanrooms. Monitoring helps identify and control potential sources of contamination, allowing for swift corrective actions if any deviations from the desired cleanliness levels are detected. State-of-the-art monitoring systems are utilized in our cleanrooms to measure various parameters, such as airborne particle counts, microbial counts, temperature, humidity, and differential pressure. These monitoring systems provide real-time data, enabling personnel to respond promptly to any anomalies.
Validation and Qualification
Validation and qualification are essential steps to demonstrate that aseptic processes are consistently effective and capable of producing sterile products. Cleanrooms and equipment must undergo extensive validation processes to ensure they meet the necessary standards and regulatory requirements. Validation involves conducting comprehensive tests and assessments to demonstrate the effectiveness of aseptic processes in preventing contamination. Qualification, on the other hand, ensures that all equipment used in aseptic processing operates within specified parameters and does not compromise the sterile environment.
Cleaning and Disinfection
Thorough and frequent cleaning and disinfection procedures are indispensable in maintaining the pristine environment of cleanrooms. Proper cleaning protocols, using suitable disinfectants, are employed to eliminate potential contaminants from surfaces, equipment, and workstations. Cleanroom personnel must strictly adhere to established cleaning schedules and use validated cleaning agents to ensure effective decontamination. In addition, regular monitoring and auditing of cleaning processes are conducted to verify their efficacy and compliance with aseptic standards. These measures not only mitigate the risk of contamination but also contribute to the production of safe, high-quality, and reliable sterile products, ultimately safeguarding the health and well-being of patients worldwide.
Conclusion
Aseptic processing stands as an imperative safeguard for producing sterile products of uncompromised quality. The pivotal role of ICS cleanrooms in maintaining controlled environments cannot be overstated, acting as barrier against microbial contamination throughout the manufacturing journey. The collaborative efforts of cleanrooms and skilled professionals ensure the integrity, stability, and safety of pharmaceutical products, thereby upholding the highest standards of patient care and industry excellence.