Electronic and Semiconductor Cleanrooms
Cleanrooms are used in the electronics and semiconductor industry to prevent particles and contaminants from interfering with the highly sensitive manufacturing process, ensuring the quality and reliability in precision tubing delivering ultra pure gasses remains uncompromised. Controlling the level of airborne particulates enables the production of high-quality products by minimizing the risk of defects or failures.
Talk to an expertLet us help you find the right cleanroom
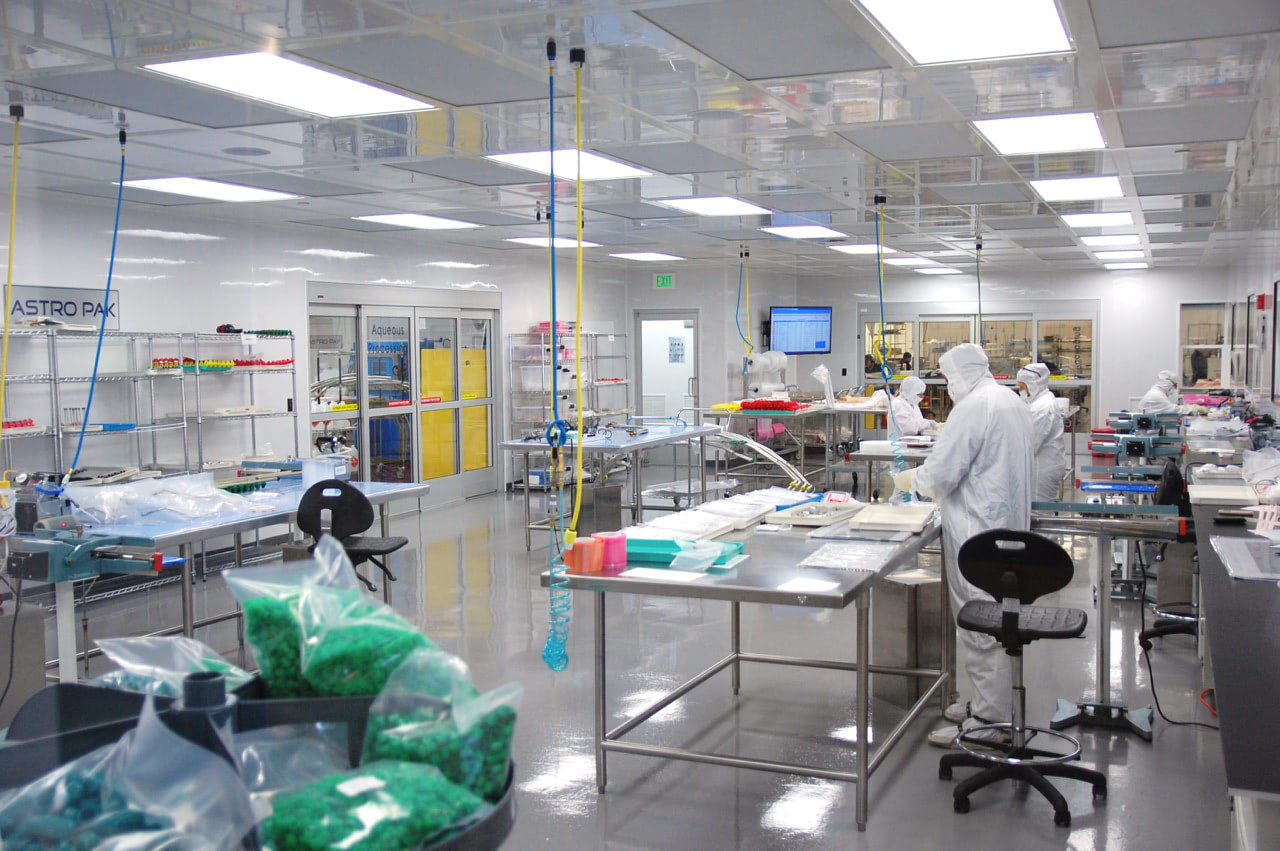
Standards, Certifications, and Control Measures
- ISO 14644: It provides guidelines for cleanroom design, construction, and operation and specifies cleanliness levels.
- Federal Standard 209E: It defines cleanliness levels of cleanrooms by the number of particles per cubic foot of air.
- Semiconductor Equipment and Materials International (SEMI) Standards: These are industry standards that specify the requirements for equipment used in the semiconductor manufacturing process, including cleanliness levels.
- Occupational Safety and Health Administration (OSHA): It sets and enforces workplace safety standards, including those for cleanrooms, to protect workers from hazards.
Cleanrooms can be certified by a third party in many ways. Some common options include:
- Particle counting: Measures airborne particle concentration using laser particle counters.
- Airflow velocity measurement: Measures airflow velocity using an anemometer or similar device.
- Filter Integrity test: Ensures the filter does not have pin holes that could be compromising the overall performance.
- Smoke studies: Introduces smoke to observe airflow movement and design.
- Pressure differential measurement: Measures pressure differential to ensure proper isolation from outside contamination.
To maintain the standard of this certification, a cleanroom should be checked – at 6 month intervals for ISO 5 and 12 month intervals for ISO 6 and above – using the same or similar methods to the certification process.
- Use of appropriate personal protective equipment (PPE)
- Establishment and maintenance of a cleanroom environment that adheres to standards and regulations
- Implementation of proper cleaning procedures
- Proper handling and storage of materials and equipment
- Proper cleanroom balancing to maintain positive cascading pressure (from the main cleanroom to the anterooms then to the outside)
- Regular monitoring and testing of the cleanroom environment to ensure continued compliance and minimize the risk of contamination.
Experience the ICS difference.
Expert Cleanroom Design and Installation
ICS is a top-tier cleanroom supplier that specializes in creating intentional and customized designs to meet clients' specific needs within industry-leading timeframes. All our cleanrooms are fully certified by third-party organizations, ensuring the highest standards of cleanliness and quality. With six decades of experience in cleanroom construction, we have won notable awards, including the Department of Energy's Small Business of the Year.
Frequently asked questions
Cleanrooms in electronic and semiconductor manufacturing must adhere to strict standards to maintain the highest levels of cleanliness and prevent contamination. Key standards used in the industry include ISO 14644-1, which defines air cleanliness classifications, Federal Standard 209E, SEMI Standards covering design, construction, and operation, and Good Manufacturing Practice guidelines. Best practices such as equipment maintenance, PPE usage, and quality control and testing procedures may also be used to ensure product quality.
Cleanrooms are used in electronic and semiconductor manufacturing to maintain a controlled environment with low levels of airborne particles, dust, and other contaminants. This is critical to ensuring the quality and reliability of electronic components and semiconductors. Cleanrooms are used throughout the manufacturing process, from the initial construction of fabs, to the fabrication of wafers and substrates. They are also used in research and development, testing, and quality control to ensure that products meet industry standards and regulatory requirements.
- Soft-Wall Cleanrooms (Barrier Isolators): These cleanrooms are used in the electronic and semiconductor industry to prevent contamination of sensitive materials, such as advanced microprocessors and memory chips.
- Hard-Wall Cleanroom Suites: Multiple connected cleanrooms are used in the industry to manufacture different products in different environments while maintaining the overall production process's integrity.
- Mobile Cleanrooms: These cleanrooms are also used in the electronic and semiconductor industry and can be transported to different locations for temporary production needs, such as during a shortage of critical electronic components, emergency response, or facility maintenance.
Each type of cleanroom is designed to meet specific requirements and equipped with specialized equipment, materials, and procedures to maintain the cleanliness and sterility of the environment necessary for electronic and semiconductor manufacturing.
The ISO standard for cleanrooms used in electronic and semiconductor manufacturing is ISO 14644-1. ISO 14644-1 provides a standardized system for measuring and reporting the concentration of airborne particles of various sizes in cleanrooms. The standard defines cleanliness classes based on the number of particles per cubic meter of air. In the electronic and semiconductor industry, ISO 14644-1 is often used to classify cleanrooms according to the minimum cleanliness levels required for specific manufacturing processes. This helps to ensure that the cleanroom environment is controlled to prevent contamination and meet industry standards.
Q: What are semiconductors and why must they be handled within a cleanroom?
A: Semiconductors are made of pure silicon and are prized for their special conductive behavior, which is vital for manufacturing computer chips and circuitry. Semiconductor chips are fragile and must be handled within a cleanroom to ensure strict control over the chip manufacturing environment and prevent any inconsistencies that could compromise their safety and effectiveness.
Q: What is the CHIPS and Science Act and how has it impacted the semiconductor industry?
A: The CHIPS and Science Act is a U.S. government act that authorizes nearly $52 billion in government subsidies for U.S. semiconductor manufacturing and research, as well as an estimated $24 billion in investment tax credits for semiconductor chip manufacturers. The act has impacted the semiconductor industry by providing funding and resources for semiconductor projects, allowing for expansion of semiconductor chip manufacturing companies and the need for more cleanrooms.
Q: What industries and applications require semiconductor cleanrooms?
A: Semiconductor cleanrooms are required in industries and applications where maintaining quality and purity in semiconductor chip manufacturing is crucial, such as computer and cell phone manufacturing, automotive manufacturing, aerospace and defense manufacturing, robotic and automated equipment manufacturing, household appliance manufacturing, and biotechnology manufacturing.
Q: What are the requirements for semiconductor cleanroom classifications?
A: In most cases, semiconductor cleanrooms must comply with ISO 14644-1 Class 4-6 requirements, which stipulates a maximum allowed particle count between 352-35,200 particles 0.5μm or smaller. They must also meet the requirements of ISO 14644-2, which imposes a quality control system to maintain these standards. Depending on their unique application, semiconductor cleanrooms will also likely have to meet some industry-specific requirements, such as ASTM standards for automotive applications and NASA standards for aerospace applications.
Q: What are some important aspects to consider in semiconductor cleanroom design?
A: Important aspects to consider in semiconductor cleanroom design include specially trained operators and safety protocols, a high level of air quality and filtration systems, protection against static, humidity, and out-gassing, and compliance with industry-specific requirements in addition to ISO standards.