Aerospace and Defense Cleanrooms
Our Cleanrooms are used extensively in the manufacturing and assembly of satellites, military equipment, spacecraft, and other sensitive, high-tech components. They provide a precisely controlled environment that minimizes the risk of contamination and ensures the highest level of quality and reliability to prevent potentially catastrophic failures.
Talk to an expertLet us help you find the right cleanroom
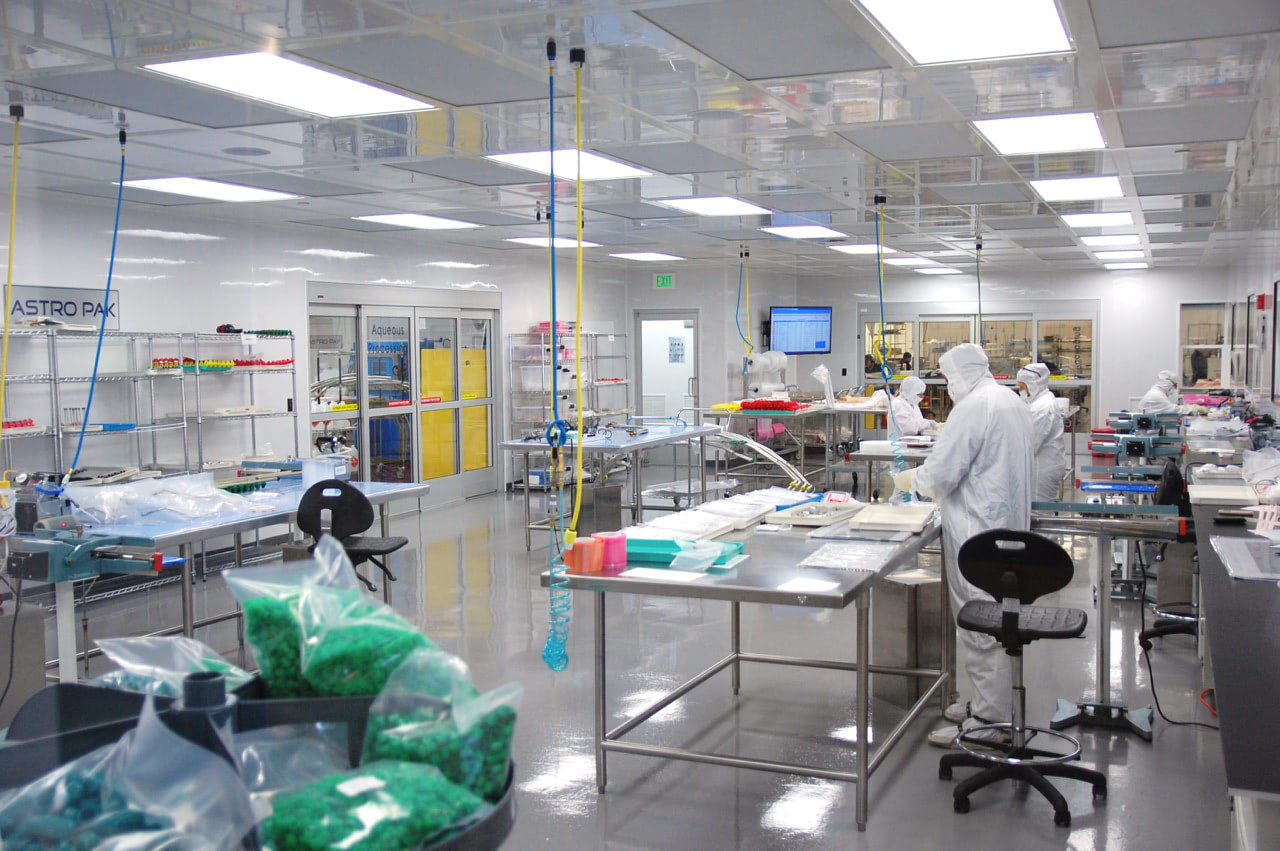
Standards, Certifications, and Control Measures
- ISO 14644: It provides guidelines for cleanroom design, construction, and operation and specifies cleanliness levels.
- Federal Standard 209E: It defines cleanliness levels of cleanrooms by the number of particles per cubic foot of air.
- Clean Air Act: It regulates air pollution, including emissions from manufacturing processes, and requires compliance from aerospace and defense manufacturers.
- National Aerospace Standard (NAS) 1638: It specifies contamination control requirements in aerospace manufacturing facilities.
- Military Standard (MIL-STD) 1246C: It provides guidelines for material selection and use in cleanrooms.
- Occupational Safety and Health Administration (OSHA): It sets and enforces workplace safety standards, including those for cleanrooms, to protect workers from hazards.
Aerospace and Defense Cleanrooms can be certified by a third party in many ways. Some common options include:
- Particle counting: Measures airborne particle concentration using particle counters.
- Airflow velocity measurement: Measures airflow velocity using an anemometer or similar device.
- Smoke studies: Introduces smoke to observe airflow movement and design.
- Pressure differential measurement: Measures pressure differential to ensure proper isolation from outside contamination.
To maintain the standard of this certification, a cleanroom should be checked – at 6 month intervals for ISO 5 and 12 month intervals for ISO 6 and above – using the same or similar methods to the certification process.
- Use of appropriate personal protective equipment (PPE)
- Establishment and maintenance of a cleanroom environment that adheres to standards and regulations
- Implementation of proper cleaning and disinfection procedures
- Proper handling and storage of materials and equipment
- Proper cleanroom balancing to maintain positive cascading pressure (from the main cleanroom to the anterooms then to the outside)
- Regular monitoring and testing of the cleanroom environment to ensure continued compliance and minimize the risk of contamination.
Experience the ICS difference.
Expert Cleanroom Design and Installation
ICS is a top-tier cleanroom supplier that specializes in creating intentional and customized designs to meet clients' specific needs within industry-leading timeframes. All our cleanrooms are fully certified by third-party organizations, ensuring the highest standards of cleanliness and quality. With six decades of experience in cleanroom construction, we have won notable awards, including the Department of Energy's Small Business of the Year.
Frequently asked questions
The cleanroom requirements for aerospace applications will depend on the specific manufacturing or assembly process being carried out. However, aerospace applications often require cleanrooms with very high levels of cleanliness to ensure the quality and reliability of the products being produced. In general, a cleanroom for aerospace applications will need to have:
- High-efficiency particulate air (HEPA) filters to remove particles from the air.
- Controlled airflows to minimize the introduction of particles and contaminants.
- Proper gowning procedures for personnel entering the cleanroom.
- Regular monitoring and testing of the cleanliness level to ensure compliance with industry standards.
For more specific questions regarding your cleanroom and specification, please call us.
Aerospace and defense manufacturing must comply with cleanroom standards and regulations such as ISO 14644, Federal Standard 209E, MIL-STD-1246C, NASA-STD-6001, and AS9100, as well as applicable regulations from regulatory bodies such as the FAA and DoD, to ensure the safety and reliability of their products. Beyond ISO 14644 and FE 209E, many Aerospace specifications use a system of Class ratings (1,000, 10,000, etc.) as a relic of post-war Aerospace manufacturing. Although the industry has begun transitioning to the ISO standard, the Class standards are important to keep in mind for standardization.
- ISO 14644: A widely recognized international standard that establishes the requirements for cleanroom design, operation, and monitoring.
- Federal Standard 209E: A U.S. standard that specifies the requirements for cleanroom classes based on the number of particles per cubic foot of air.
- MIL-STD-1246C: A U.S. military standard that establishes the requirements for cleanrooms in defense manufacturing, covering topics such as cleanroom design, maintenance, and testing.
- NASA-STD-6001: A standard developed by NASA that establishes the requirements for cleanroom operations in the aerospace industry, covering topics such as cleanroom design, gowning procedures, and air quality monitoring.
- AS9100: A quality management standard specific to the aerospace industry that includes requirements for cleanroom operations, such as the need for a cleanroom management system and regular monitoring and testing of the cleanroom environment.
- Cleanliness requirements: The level of cleanliness required for the specific aerospace or defense application must be determined, as this will impact the design of the cleanroom.
- Size and layout: The size and layout of the cleanroom must be designed to meet the specific manufacturing process requirements while maximizing the use of available space. Cleanroom size (cubic volume) will also impact the HVAC requirements, which will have an effect on the efficiency of the cleanroom.
- Air filtration and ventilation: Proper air filtration and ventilation are critical in cleanroom design to ensure that the cleanroom meets the necessary cleanliness requirements. Ensuring the cleanroom has enough capacity to ”breathe” is critical to allow for a proper air change rate.
- Gowning and personnel flow: Proper gowning procedures and personnel flow must be established to minimize the introduction of particles and contaminants into the cleanroom.
- Equipment and materials: Assessing the equipment and materials used in the manufacturing process is critical to helping maintain the clean environment. One example is pneumatically operated equipment within the cleanroom. If general, unfiltered air or lightly filtered air is being used to operate a tool within the cleanroom, the exhaust may cause a great amount of contamination. To avoid this it would be best to add a point of use millipore filter or use a clean and dry inert gas like nitrogen.
- Monitoring and control: The cleanroom must have a monitoring and control system in place to ensure that the necessary cleanliness requirements are maintained. Without an environmental monitoring system, the cleanroom environment might give no degradation or failure warning before your next certification.
The cleanroom certification process typically involves the following steps:
- At-rest Certification: The cleanroom is tested before any manufacturing operations begin to add a "control test" to make sure the cleanroom is operating as expected without people or equipment operating.
- Dynamic Certification: The cleanroom is tested during manufacturing operations to ensure that it meets the required cleanliness standards while in use.
- Remediation: If any issues are identified during certification testing, corrective actions are taken to bring the cleanroom into compliance. This can be as simple as rebalancing the cleanroom, and patching a HEPA filter or as complicated as a full redesign.
- Final testing: Once any necessary remediation has been completed, the cleanroom is retested to verify that it meets the required cleanliness standards.
- Ongoing monitoring: After certification, handheld particle counters can be used in a weekly standard operating procedure test to ensure that the cleanroom continues to meet the necessary cleanliness standards.
Cleanroom certification is important in aerospace and defense manufacturing for several reasons:
- Quality assurance: Cleanroom certification ensures that the products being produced meet the necessary cleanliness standards and are of high quality.
- Safety: Cleanroom certification helps to ensure that the manufacturing process is safe for personnel and the environment.
- Compliance: Many aerospace and defense contracts require cleanroom certification as a condition of the contract.
- Liability: Cleanroom certification provides an additional layer of protection against liability in the event of product failure.