Cleanrooms For Medical Device Manufacturing
Cleanrooms are used in the medical device manufacturing industry to manufacture products in an aseptic or controlled environment. They are used for manufacturing, packaging, sterilization, and quality control testing of medical devices. Cleanrooms play a critical role in ensuring patient safety by preventing contamination and maintaining quality standards.
Talk to an expertLet us help you find the right cleanroom
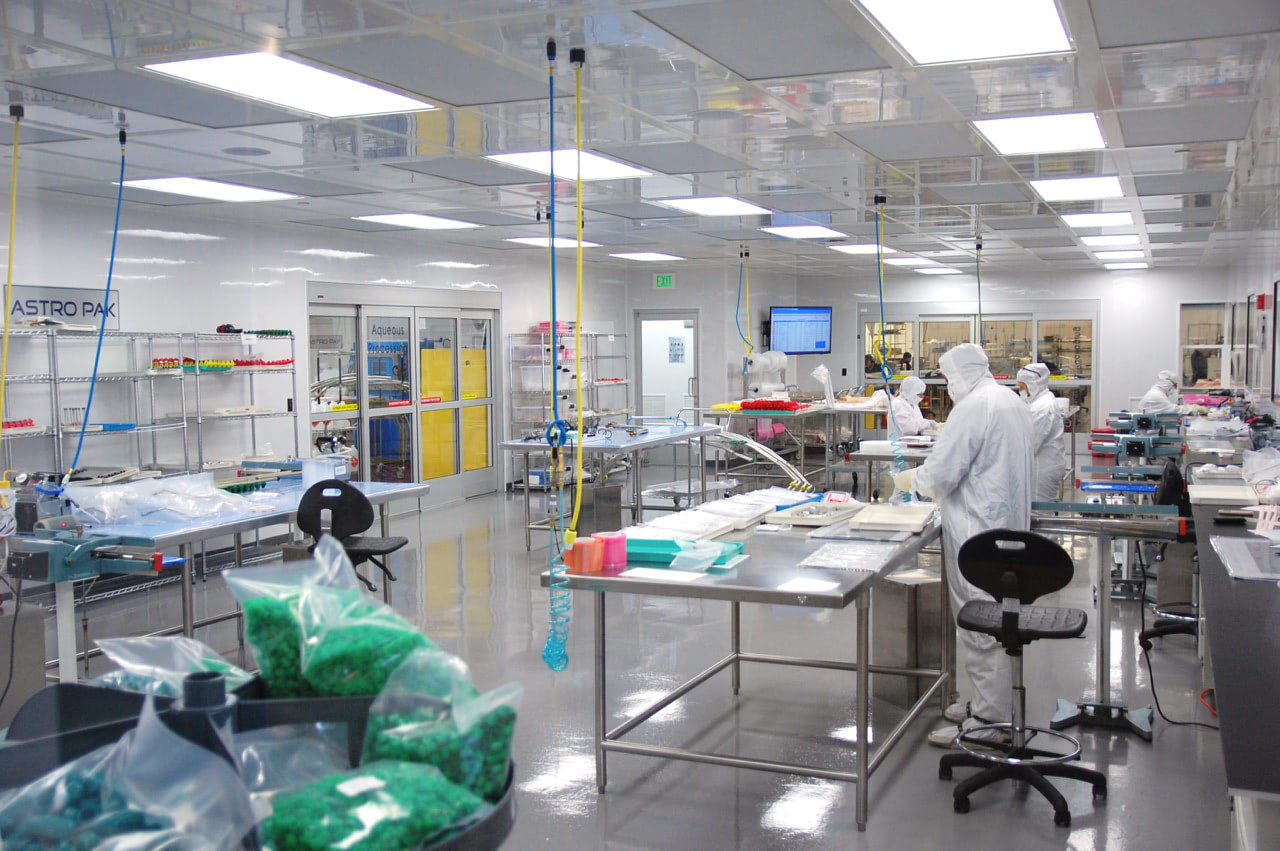
Standards, Certifications, and Control Measures
- ISO 14644-1: Specifies the maximum allowable concentration of particles in the air and outlines testing and monitoring procedures to ensure air cleanliness in cleanrooms and controlled environments.
- ISO 13485: The international standard for quality management systems in medical device manufacturing, establishing requirements for the entire product lifecycle from design and development to production and distribution.
- FDA cGMP: The FDA's Current Good Manufacturing Practices (cGMP) regulations set out the minimum requirements for the design, production, testing, and distribution of medical devices in the United States.
- EU MDR: The European Union's Medical Devices Regulation (MDR) sets out the requirements for the design, production, testing, and distribution of medical devices within the EU.
- IEST-RP-CC018: This is the Institute of Environmental Sciences and Technology Recommended Practice for Cleanroom Housekeeping - Operating and Monitoring Procedures.
Medical Device Manufacturing Cleanrooms can be certified by a third party in many ways. Some common options include:
- Particle counting: Measures airborne particle concentration using particle counters.
- Airflow velocity measurement: Measures airflow velocity using an anemometer or similar device.
- Fiulter Integrity Testing: ensure there are no pin holes that are compromise the performance of the HEPA filter.
- Smoke studies: Introduces smoke to observe airflow movement and design.
- Pressure differential measurement: Measures pressure differential to ensure proper isolation from outside contamination.
- Microbial sampling: Tests for presence of microorganisms or CFU (Colony Forming Units) to ensure cleanroom is free from viable contamination.
To maintain the standard of this certification, a cleanroom should be checked – at 6 month intervals for ISO 5 and 12 month intervals for ISO 6 and above – using the same or similar methods to the certification process.
- Use of appropriate personal protective equipment (PPE)
- Establishment and maintenance of a cleanroom environment that adheres to standards and regulations
- Implementation of proper cleaning and disinfection procedures
- Proper handling and storage of materials and equipment
- Proper cleanroom balancing to maintain positive cascading pressure (from the main cleanroom to the anterooms then to the outside)
- Regular monitoring and testing of the cleanroom environment to ensure continued compliance and minimize the risk of contamination.
Experience the ICS difference.
Expert Cleanroom Design and Installation
ICS is a top-tier cleanroom supplier that specializes in creating intentional and customized designs to meet clients' specific needs within industry-leading timeframes. All our cleanrooms are fully certified by third-party organizations, ensuring the highest standards of cleanliness and quality. With six decades of experience in cleanroom construction, we have won notable awards, including the Department of Energy's Small Business of the Year.
Frequently asked questions
Cleanroom requirements for medical device manufacturing are defined by regulatory agencies such as the U.S. Food and Drug Administration (FDA) and the International Organization for Standardization (ISO). These requirements include cleanroom classification, design, maintenance, personnel and equipment requirements, and quality control measures.
The two main Quality Management Systems (QMS) used for medical device manufacturing are:
- ISO 13485: This is an internationally recognized standard that outlines the requirements for a QMS specific to medical devices. It covers all aspects of the manufacturing process, including design and development, production, installation, and servicing of medical devices. ISO 13485 focuses on risk management and ensuring compliance with regulatory requirements.
- 21 CFR Part 820: This is a regulation issued by the U.S. Food and Drug Administration (FDA) that outlines the QMS requirements for medical device manufacturing in the United States. It covers similar aspects as ISO 13485, including design controls, production controls, and device history records. 21 CFR Part 820 also emphasizes the importance of device validation, process validation, and design verification
A cleanroom is a controlled environment that is designed to minimize the risk of contamination in the manufacturing process. It is a specially designed room or facility where the level of airborne particles, such as dust, microbes, and other contaminants, is controlled and reduced to an acceptable level.
In medical device manufacturing, cleanrooms are essential to ensure the quality and safety of the devices produced. Medical devices are often used in critical applications, and any contamination during the manufacturing process can have serious consequences for patients. Cleanrooms help to minimize the risk of contamination by controlling the level of particles in the air, and by providing a controlled environment that is easy to clean and maintain.
There are different types of cleanrooms for medical device manufacturing, and each is classified based on the maximum allowable number of particles per cubic meter of air at a specified particle size. The classification of cleanrooms is determined by the ISO standard 14644-1 or the U.S. Federal Standard 209E and ranges from ISO 4-8 for the ISO specification and Class 10-100,000 for the FS209E specification. In addition to these classifications, there are also specialized cleanrooms that are designed for specific manufacturing processes or applications, such as sterile filling rooms for aseptic filling of drugs and isolators for handling hazardous materials. The choice of cleanroom classification will depend on the type of medical device being manufactured and the level of cleanliness required for the device to meet regulatory requirements and ensure patient safety.
The classification of cleanrooms is determined by the ISO standard 14644-1 or the U.S. Federal Standard 209E. The types of cleanrooms for medical device manufacturing include:
- ISO Class 5: This is the cleanest classification of cleanrooms typically seen in the medical device industry and is suitable for manufacturing Class 3 medical devices such as implantable devices and sterile drug products. The maximum allowable number of particles per cubic meter of air for particles equal to or larger than 0.5 microns is 3,520.
- ISO Class 6: This classification is suitable for manufacturing medical devices that require a high level of cleanliness, such as surgical instruments and electronic devices. The maximum allowable number of particles per cubic meter of air for particles equal to or larger than 0.5 microns is 35,200.
- ISO Class 7: This classification is suitable for manufacturing medical devices that require a moderate level of cleanliness, such as catheters and tubing. The maximum allowable number of particles per cubic meter of air for particles equal to or larger than 0.5 microns is 352,000.
- ISO Class 8: This classification is suitable for manufacturing medical devices that require a low level of cleanliness, such as non-invasive devices and packaging materials. The maximum allowable number of particles per cubic meter of air for particles equal to or larger than 0.5 microns is 3,520,000.